Sealing Success: Overmolding for More Secure Connections
Overmolding is the hard-working protection solution for electronic components in the field. Innovative technologies ensure connections in medical, industrial, and other harsh environment applications.
Overmolding is the process of encasing electronic components with a covering to create a single, integrated part. The process is done mainly for environmental protection, ease of installation, and to meet desired performance requirements. Overmolding is used, for example, to secure the transition from a cable to a connector body or to protect electronic devices. “The overmold does a very good job of providing protection against any type of environmental issues that could cause degradation of the electrical connection,” said Ken Dowhower, senior development engineer and group leader for industrial field connection products, Phoenix Contact USA.
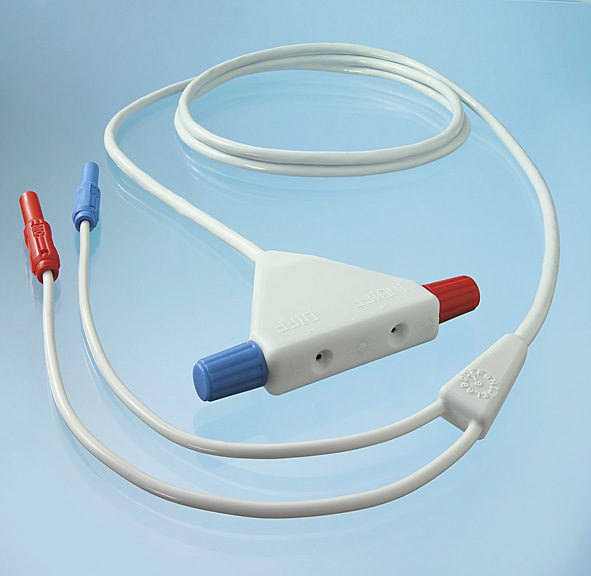
Medical cable assembly for heart stimulation from Axon’ Cable. Overmolding provides robust and tailor-made mechanical protection for example for the cable/connector interface, which is traditionally the weakest point of cable assemblies, as well as shaping, strain relief, sealing for airtightness and watertightness, absorption of repeated flexes, provision of fixing points, protection of shielding termination (EMC), and improvement of the overall look of the harness.
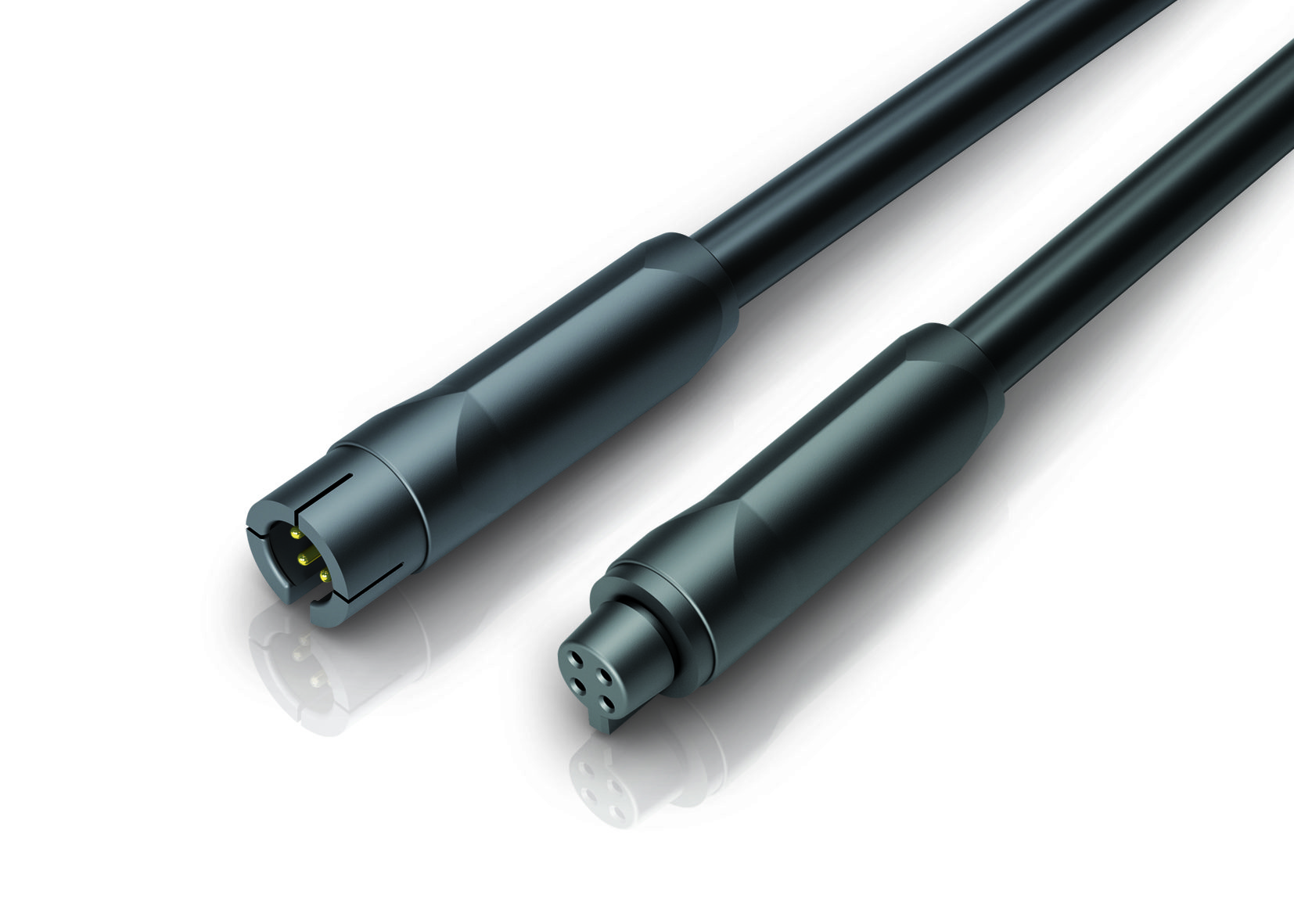
Metering and handheld operating devices in hygiene-critical application areas, such as in medical equipment, require designs optimized for safe handling as well as resistance to dirt. binder has therefore equipped its 709 and 719 snap-in series with a new overmolding that supports single-handed mating and unmating, but also improves resistance to contamination.
Overmolding is useful in many markets and applications, including machine building, factory automation, industrial vehicles, construction vehicles, agriculture, robotics, automotive, food and beverage, and medical.
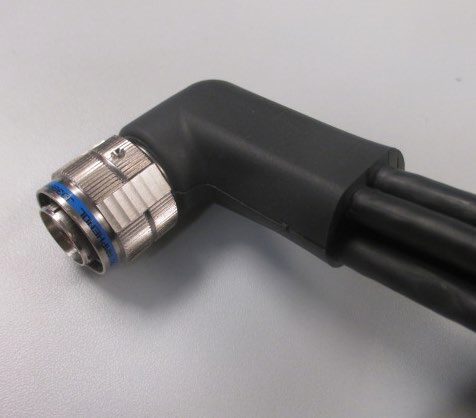
Interconnect cable assembly solution with a multi-cable overmolded strain relief from Amphenol Pcd.
As a secondary process, overmolding occurs after injection molding, and is sometimes called insert molding or co-injection molding. The process starts by securely suspending an interconnect, or other item, in another mold. “This is trickier technology because nothing can move around,” said Rich Newman, cable engineering manager at Amphenol Pcd. Ironically, the process itself subjects the components to some of the conditions that overmolding is designed to protect against. Manufacturers like Amphenol Pcd have proprietary technology that ensures the components are protected during the overmolding process as well as after. “In general, when insert molding connectors or electronics, you have a lot of heat and a lot of pressure involved that basically can damage all the components inside. Protecting the internals that are being overmolded including the wires, the electronics, and anything else that comes into play inside of the connector, is a critical part of the process.”
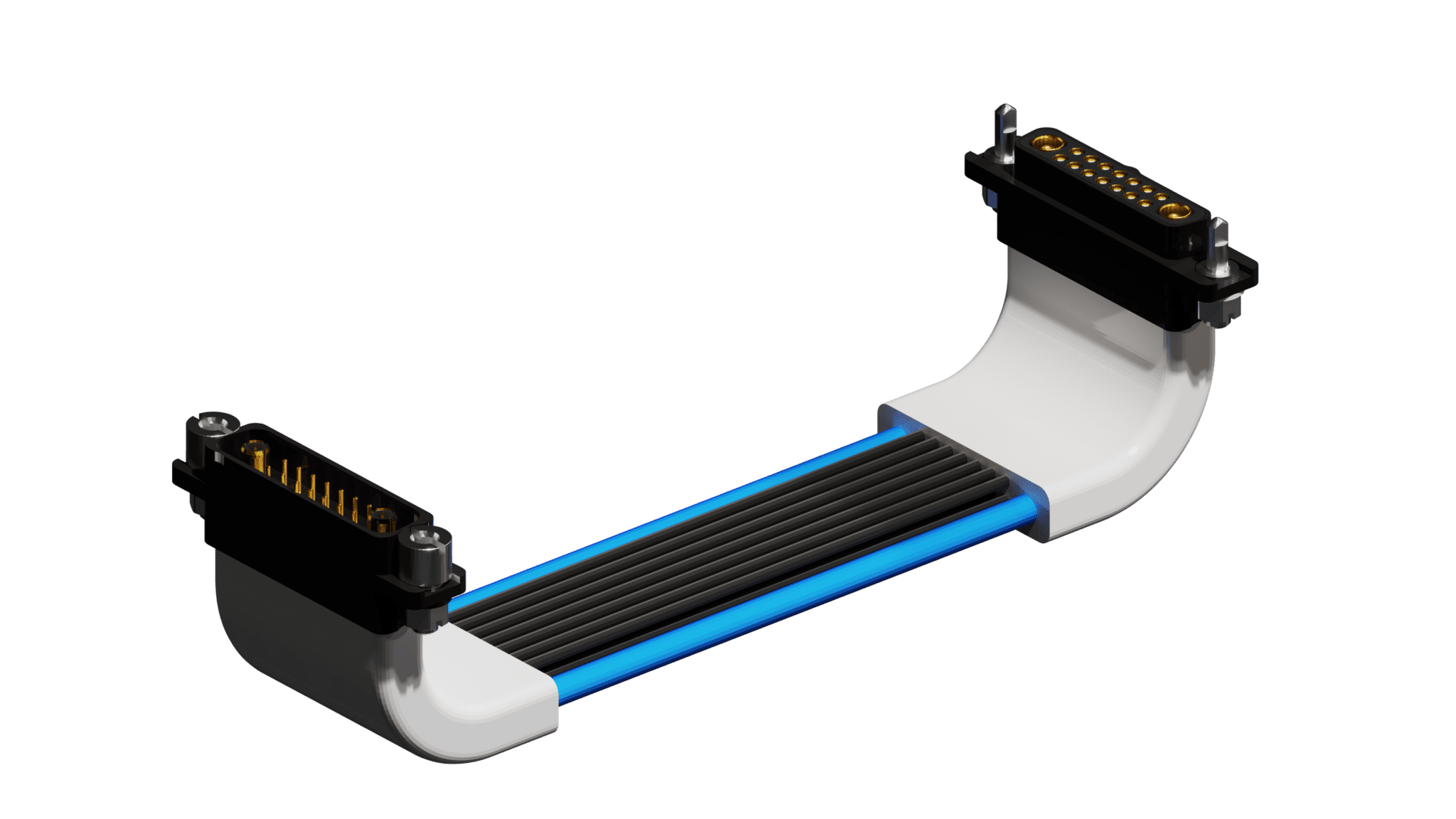
Nicomatic specializes in cable overmolding to provide optimal protection for electronic assemblies. Flexible overmolding is made of silicone-based resin, and rigid overmolding is achieved through low-pressure injection and hotmelt.
“Part of a good overall design is to make sure that the overmold adheres well to the connector body and cable jacket so it doesn’t dislodge and come loose after multiple mating and unmating cycles. At Phoenix Contact we do a tensile test of the adhesion to see how much force it takes to dislodge the jacket from the overmold. Ideally, the jacket should break before it is dislodged from the overmold,” said Dowhower.
Materials
Overmolding uses pliable materials to protect the rigid connector materials (metal and plastic), the cable, and the connection. The materials are chosen for their different properties to meet industry standards such as UL. Thermoplastic elastomer (TPE), thermoplastic polyurethane (TPU), and polypropylene are commonly used overmold materials.
Flammability and temperature ratings are important for certain applications. “We use the polypropylene more for signal and data connections where flammability isn’t quite as important of a concern,” said Dowhower. “The thermoplastic polyurethane has a higher flammability rating, so it’s more useful on higher power connections. Running more current through it or when there’s a higher risk of something shorting out can create heat, which could potentially cause a fire, so we have to have a material that extinguishes itself.”
These materials also have different temperature ratings. “Most of our standard assemblies are rated 90 °C, but we also have, for example, an outdoor line M12. Based on that application, which might include going into a harsher environment, a higher temperature is needed. So that one typically gets rated to around 105 °C,” said Jeremy Andrews, product marketing manager – industrial field connectivity, Phoenix Contact USA.
Overmolding provides many benefits
Ease of installation and cost effectiveness
When a high quantity of cables is needed, overmolded cordsets from the factory provide a solution that can basically plug and play, saving a lot of time and labor compared to field assembling components, said Andrews.
In terms of protection, Nick O’Leary, product specialist for cable assemblies at Amphenol Pcd, explained, “It’s very similar to what a backshell provides, but it’s malleable and, usually, it’s lighter weight. It’s almost always lower cost than a backshell too.”
Durability and environmental protection
Compared to less expensive options, such as heat shrink, overmolding is ruggedized and made to last a very long time. In addition to the flammability and temperature issues, ingress protection is also a concern. “We do fluid ingress testing to make sure we get a good fluid seal. We’ll immerse the connectors in three feet of water for 30 minutes and electrically test it to make sure no water got into the overmold to cause a problem,” said Dowhower.
“There are field-assembled connectors that would have the same types of environmental protections, including an ingress protection rating of IP65 or IP67, which means they are watertight when assembled correctly and connected,” said Andrews. “However, for a lot of customers, that extra assurance of the molded cable eliminates any concern over whether it was assembled and wired correctly.”
EMI protection
Electromagnetic interference (EMI) protection is typically a requirement in military applications. EMI solutions can be incorporated into the overmolding process.
Mechanical strain relief and ergonomics
“If there is any load applied to the cable, the overmolding helps prevent electrical failure by distributing that load to the connector body and cable jacket versus the individual conductors and contacts,” Dowhower said. “The geometry of the overmold can be tailored to be more ergonomic for gripping and manipulating the cables. This can include adding features to prevent slipping, for example in a medical setting when the user is wearing gloves.”
Pushing limits: the future of overmolding
As with much of technology today, customers want overmolding that allows them to push limits. “Some product areas require higher temperatures so Amphenol Pcd is adapting to different technologies and different materials to meet those requirements,” said Newman. “Customers want more seals to go in deeper water and temperatures are starting to creep up into the 175-200 °C range. That requires getting into new materials like silicones, fluorosilicones, and high-performance fluoroelastomers.” Greater chemical resistance is another area customers are looking to address.
Phoenix Contact works with a lot of industry standard M8s and M12s. However, a new area for overmolding is M12 power. “M12 power, still relatively new to the market, allows higher power to pass through the M12 form factor. But when it comes to the overmolding, this product family has a little bit larger grip body. The material is slightly different, based off the application and the process to mold those cables,” said Andrews. Another new development from Phoenix Contact is advanced shielding technology. “That overmold process happens in steps: a pre-mold, a liquid metal to form the shield (almost like a metal molded process), and the traditional overmold of the connector after that.”
To learn more about the companies mentioned in this article, visit the Preferred Supplier pages for Amphenol Pcd, Phoenix Contact, Nicomatic, Axon Cable and binder.
Like this article? Check out our other Technology Trends articles, our Medical Market Page, and our 2024 Article Archive.
Subscribe to our weekly e-newsletters, follow us on LinkedIn, Twitter, and Facebook, and check out our eBook archives for more applicable, expert-informed connectivity content.
- Meet the Engineer: When Art and Engineering Collide - April 30, 2024
- What are MIL-DTL-26482 connectors? - April 30, 2024
- DIN Rails and Terminal Blocks Product Roundup - April 30, 2024