Construction Vehicles Go Electric
As the construction industry embraces electrification, OEMs are discovering it’s not as simple as repurposing the technology used in passenger vehicles. Connector suppliers are addressing the unique challenges this shift entails.
The off-road transportation sector, which includes construction, mining, and agriculture vehicles, is embracing electrification due to the benefits it affords. However, certain challenges have become evident. For starters, much of what has been done with electric passenger vehicles cannot not simply transfer. Here’s why.
The vehicles in this market are typically much larger and heavier than passenger cars, and require much greater current and voltage, explained Daniel Domke, product manager, e-mobility solutions at TE Connectivity. “A lot of these connectors and cables are exposed and visible from the outside. That means their requirements for mechanical robustness are much higher compared to a passenger car,” he said. “These vehicles are subjected to repeated high-pressure washing so we need to make sure that no water will be forced or pushed into the connectors, which is a safety relevant aspect. Within these vehicles, we often still have hydraulic oil or other chemicals, so we need to make sure that all these connectors fulfill all the requirements over their lifetime.” This includes the ability to withstand extreme temperatures and vibration for extended periods, and resist chemicals, corrosion, dust, dirt, and water ingress.
These are working assets. Unlike passenger vehicles, which tend to be driven for only a small percentage of each day, their time in use is going to be maximized, regardless of the environments they are in, said Mark Brubaker, product manager for data connectivity at TE. “Compared to passenger cars, these assets are exposed a lot longer to things like salt and grime.”
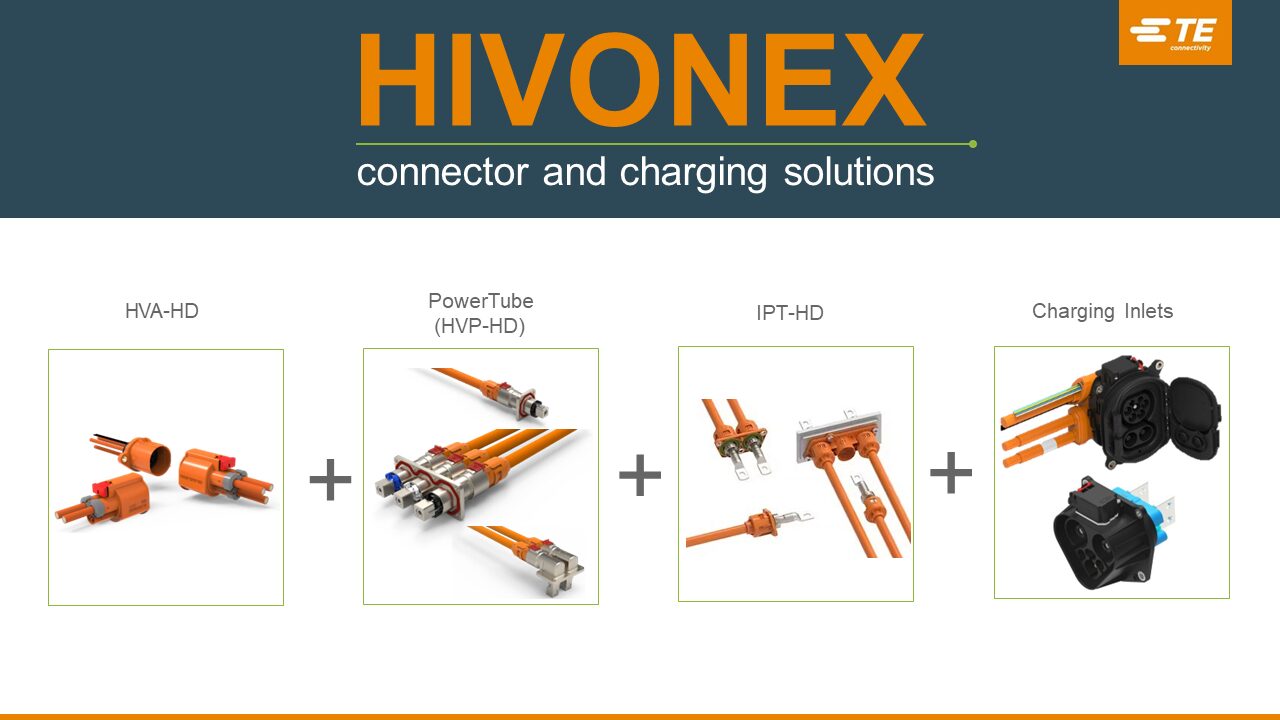
TE has created a product line specifically for the commercial off-road market, rather than try to make existing passenger car or industrial connectors fit this segment. “That means for every kind of current or wider cross section that we would need to cover, we basically have our own product that we offer,” said Domke.
What’s driving this market?
Multiple factors make electrification advantageous for this market. “In big cities, like Paris for example, and in some smaller villages, to get a construction contract, you must guarantee that the equipment you use is fully electric,” said Domke. Diesel engines are loud and, therefore, can only run during the day. Electrification eliminates that noise, so the available work time can be extended to nearly 24 hours per day. This is especially useful in city construction to reduce the days of disruption to the area and expand the areas where this work can be done.
In addition to noise, diesel engines generate a lot of exhaust and CO2 emissions that negatively impact air quality. Mitigating that exhaust in the surrounding area is a complex undertaking that is eliminated with electrified equipment. “This is where we see almost every OEM is moving towards with at least a portion of their segment to be electrified, and they are extending it step by step, starting with smaller- and medium-size equipment. Some of the bigger companies have already converted their really large equipment, excavators, and so on,” said Domke.
Maintenance is a huge issue for small equipment rental companies, because this equipment takes a lot of abuse. Electric vehicles eliminate much of the maintenance problem areas: the diesel engine itself, much of the moving components, and the gearbox. “From a complexity standpoint, electrics are much simpler,” Domke said.
According to EDAC, some common risks associated with internal combustion engine (ICE) vehicles, such as stalling, wearing down clutch pads, or wasting energy, can be eliminated with electric motors and intelligent control systems that identify the best times to apply and cut power. For even greater control, a separate motor can be connected to each wheel of an EV. Multiple independent motors can also act as a backup. If one or two motors fail, the vehicle can still move. With ICE, a transmission or engine failure will likely cause the vehicle to seize. EVs also have a much lower latency compared to ICE vehicles. An EV can instantly respond and provide power when the accelerator is pressed, while an ICE has to wait for the additional fuel to reach the pistons before generating more power.
Modularity & scalability
When designing the connector systems for these vehicles, modularity and scalability were at the top of TE’s list, to make it easier for OEMs to have the same system on different vehicle types. For example, a hydraulic pump might be on a wheel loader or an excavator. “That may require different wire routing,” said Domke. “This is why we have now released a very modular and scalable design. We have different variants in terms of pinning, so one-, two-, or three-pin, with either a straight outlet or a 90° outlet. You can basically swap the 180° one-pin and the 90° one-pin without changing anything on the application side. That’s super important for these kinds of applications, because the OEM, in this case, can find the best configuration without necessarily changing a lot. It’s like a Lego system; they just pick and choose whatever they need and integrate it.”
On the cable side, because a lot of these wires are exposed, there is risk of, say, a rock hitting a cable and then the cable would need to be replaced. Typically, for example, a two-wire system (plus and minus) with a two- pin version means rather than one connector there is a housing with two cables. “In the case of a connector that comes with two wires, you would have to remove a lot of content. We said, let’s do only a one-pin connector,” Domke said. That means one housing with one wire. In a service case, for example, if you have to exchange something, you only exchange what is broken. That drives value for the customer, reducing inventory and increasing the serviceability of the overall system.”
The charging question
How the systems are charged and, on a construction site, how to ensure enough power to recharge a battery electric vehicle even if it is far from the power grid are questions that always come up. “There are very good concepts now in place that reduce the anxiety of using and even buying this equipment,” Domke said. For example, a separate container full of batteries with a solar system on top can act as a stationary battery pack to recharge the vehicles. “We try to support and explain that this use case is much more efficient and maintenance is much lower. We bring in our connector systems that come with this value proposition, and then make sure that either we’ll guide them or we partner up to make sure that the overall use case is secured.”
Autonomy for safety and productivity
In the construction and agriculture space, autonomy, made possible with electrification, addresses safety and productivity. “Safety refers to sensing things around you to avoid bumping into things like people or buildings. Productivity means maximizing utilization, reducing labor inputs, being able to move dirt a quart per hour more, and minimizing disruption when, for example, a worker doesn’t show up,” said Brubaker. These capabilities don’t require full autonomy. They are supported with automated functions that address specific aspects of the vehicle running itself, such as being able to brake on its own.
The proliferation of this technology began with the automotive market, which helped pioneer a lot of technology changes that impacted cost effectiveness and scalability, and the mining industry, which has been autonomous within very constrained environments for a long time. “With those changes, it’s actually easier for agriculture and construction OEMs to adopt the new technology and create applications that increase productivity and safety, such as different types of controlling electronics, cameras or sensors, or antennas and other types of telemetry units. That extends to the connectors and the cables that connect those devices as well. This transformation also makes it commercially viable,” said Brubaker. “The result is more data intensive devices. We have to make sure that those communication protocols can translate from the automotive space to here. All the environmental dynamics for high voltage, high power applications have a similar impact on the data side to enable these types of autonomy trends.”
To learn more about the companies mentioned in this article, visit the Preferred Supplier pages for EDAC and TE Connectivity.
Like this article? Check out our other EVs and HEVs and Connected Vehicles articles, our Transportation Market Page, and our 2024 Article Archives.
Subscribe to our weekly e-newsletters, follow us on LinkedIn, Twitter, and Facebook, and check out our eBook archives for more applicable, expert-informed connectivity content.
- Construction Vehicles Go Electric - June 25, 2024
- Heavy Duty Product Roundup - June 25, 2024
- What are heat sinks? - June 18, 2024